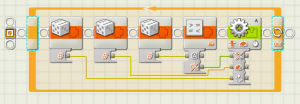
Theseย examples (ZIP) demonstrate a range of techniques for working with motors in NXT-G.
Drive for time
- This code turns on Motor A for two seconds, and then turns it off. Similar code can be made by adding motors or changing times.
Drive to black line
- There are many ways to stop a car at a black line. Using a light sensor attached to Port 1, the program takes the initial light reading, drives forward (one motor car) and waits for a difference greater than or equal to 5. Once this difference is reached, the Switch stops the NXT and exits the program.
Line follower: Switch
- This program is works like the Line Follower: Wait for Dark program but it uses a Switch. The program runs a Switch–in a infinite Loop–that runs Motor A and makes sounds when reading light. The program stops Motor A then runs Motor C for 0.25 seconds when reading dark.
Line follower: Wait for dark
- This program runs Motor A until the light reading is less than 50. Once the light reading is less than 50, Motor A stops and Motor C runs for 0.25 seconds. This processed is infinitely looped.
Lurch 1
- This code uses a Loop to turn Motor A on-and-off three times. When downloaded to a single motor car, this program will accelerate the vehicle forward in three short bursts. The number of loops can be changed by modifying the Count of “3”. Alternatively, if you want an infinite program, you can set the Control of the Loop to Forever.
Lurch 2
- This program beeps, runs Lurch-1, then beeps again.
Proportional control for position
- If a car is programmed to travel 12?, how do we know is actually traveled that distance? Often, the cars momentum will carry it past the desired location even though the motors have stopped running. The solution to this problem is a proportional control loop. By continually monitoring the distance from the desired location, the motor speed can be slowed as the car approaches. The governing formula is defined as P*(desired-current) where P is an arbitrary constant.In this program, a desired location is set at 50 degrees of the rotation sensor. This value is continually subtracted by the current rotation traveled. The difference is multiplied by two and this becomes the value of the “power” variable. The Compare Block determines the direction Motor C will travel: forward if “power” is positive, backward if “power” is negative. Thus, when the car first starts off, its current position is zero and its desired position is 50. Therefore, the power setting used is 100, which is full power forward. If the car overshoots its mark, the power setting will become negative and the car will travel in reverse. The goal of proportional control is to find a constant that will get the system to equilibrium in the shortest time with the least amount overshoot and the most accuracy.
Advanced proportional control
- The advanced proportional control program works the same way as the basic version; however, this code allows the user to vary the proportionality constant. When run, the NXT first displays the current proportionality constant that the later “power” variable will be divided by. Thus, if 4 is shown on the NXT, the proportionality constant will be ? or .25. The constant can be changed by turning the rotation sensor. Only positive values will work. After the constant is set, a press of the touch sensor will “Switch” into the proportional control loop from the basic program. Experiment with different constants. Note the difference between very small constants and very large constants.
Random motion
- The code will run Motor A in a random direction (via a Random-Comparison Block combination), at a random speed, for a random amount of time. The motor speeds will fall between 0-100 and the time will fall between 0-3 seconds.
Snake
- When run, this code will cause a car to “snake” forward in wide arcs. The length of the turns can be modified by changing either the time or motor power.
Touch sensor fork
- This code uses two very important coding commands, Switches and Loops. The touch sensor Switch causes Motor A to go forward if the touch sensor is released and backward if it is pressed. The Loop causes the Switch to loop infinitely.
Wait for push
- This code illustrates the Wait-for-Push command. When a touch sensor on Port 1 is pressed, Motor A will stop.
Wait for stall
- This code runs motors B and C until they stall. The code takes two rotation sensor readings, with a very short delay in between them. The loop exits when the difference between the two readings becomes less than a certain threshold. So if a motor slows down because it encounters an obstacle, the code will stop running the motors. A short delay in the beginning is necessary so that the motor can start moving before the rotation sensors start taking readings. Note that if the speed of the motor is decreased, the threshold for the difference needs to be lowered as well. This program was adapted from Brian Davis’ code.
Resources
- NXT-G examples – motors (ZIP)
The following two tabs change content below.

CEEO
The Tufts Center for Engineering Education and Outreach (CEEO) in Boston, Massachusetts, is dedicated to improving engineering education in the classroom, from Kindergarten to college. The Center houses faculty, staff, and graduate students from engineering disciplines and the education department.

Latest posts by CEEO (see all)
- Chair for Mr Bear - 21 August 2020
- Assistive Technology: Making Lives Easier - 20 August 2020
- Sturdy Tower - 14 June 2020
- Going the Distance - 21 May 2020
- GPS accuracy testing with LEGO bricks - 10 September 2015